Many customers will ask us a question, why the products welded by the ultrasonic welding machine we used before cannot achieve air tightness and water resistance?
For ultrasonic welding of plastic products, because of the differences in product function and function, the requirements for air tightness and water tightness of the products are different. But in the process of product production and processing, the welding process is different, and the welding effect is also different. In order to achieve airtight, watertight functions, to achieve perfect welding, MingYang ultrasonic will consider what problems?
Problem 1: Improper opening of ultrasonic waveguide fuse.
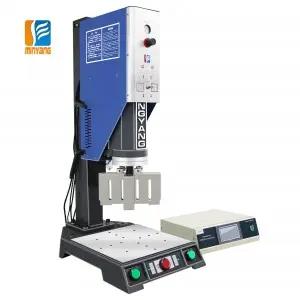
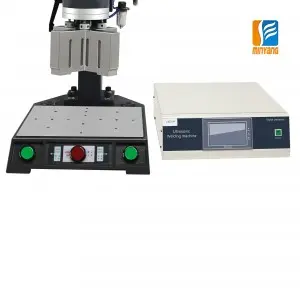
Problem 1: Improper opening of ultrasonic conductive fuse
When we want the product to achieve the function of water and airtightness, positioning and ultrasonic fuse wire are the keys to success or failure, so the considerations in product design, such as: positioning, material, material thickness, and the corresponding ultrasonic fuse wire Proportions have an absolute relationship.
In general water and airtight requirements, the height of the fuse wire should be in the range of 0.5~0.8mm (depending on the thickness of the product). Very standard, and the meat is more than 5 mm thick, otherwise it will not work well. Generally, the products that require water and airtightness are positioned and the ultrasonic fuse wire is as follows:
Bevel cut: Suitable for watertightness or welding of large plastic products.
Contact surface angle=45°, X=W/2, d=0.3~0.8mm is the best
Stepped: Suitable for watertightness or a method to prevent plastic bulging and cracking after welding
Contact surface angle=45°, X=W/2, d=0.3~0.8mm is the best.
Peak-to-valley: suitable for watertight and highly welded plastics
d=0.3~0.6mm, the height h of the contact surface changes according to the shape and size, h should be between 1-2mm.
Problem 2: Improper welding conditions
When the ultrasonic welding of the product cannot achieve water and air tightness, in addition to factors such as the ultrasonic fuse wire, the positioning of the fixture, and the positioning of the product itself, the conditions set by the ultrasonic wave are also the main reason.
Here is a more in-depth discussion of another reason (welding conditions) that affects water and air tightness. When we implement ultrasonic welding operations, seeking efficiency and speed is the most basic goal, but we often ignore the essentials of seeking efficiency. The following two conditions are discussed:
1. The descending speed and buffering are too fast: at this speed, the dynamic pressure plus the acceleration of gravity will flatten the ultrasonic fuse wire, so that the fuse wire cannot play the role of fuse guide and form a false phase fusion.
2. The welding time is too long: the plastic product receives heat energy for a long time, which not only melts the plastic material, but also causes the coking of the plastic tissue, resulting in sand holes, through which water or gas penetrates. This is the most difficult thing for ordinary production technicians to find.
If you need to know more about ultrasonic technology, please feel free to contact us. We would like to share with you some technical experience of ultrasound.
Mingyang ultrasonic equipment factory is a manufacturer and we have specialized in the production of ultrasonic welding machine for over 20 years.
Factory: Our factory is located in the China industry city–Guangdong. As a global supplier that can provide a series of plastic welding solutions, we have exported our equipment to 56 countries and won the trust of customers.
Products: Ultrasonic welding machine, ultrasonic generator, high frequency welding machine, hot melting machine, spin welding machine, other customized ultrasonic machine etc.
Certification: We have passed ISO9001 certification, and all the machines passed CE and other certifications(according to your requirement).
Service: We can provide free welding technical solutions from the beginning of the plastic project to the product is produced perfectly, and support free welding samples. we have a long-term after-sales service team.
Post time: Nov-15-2022